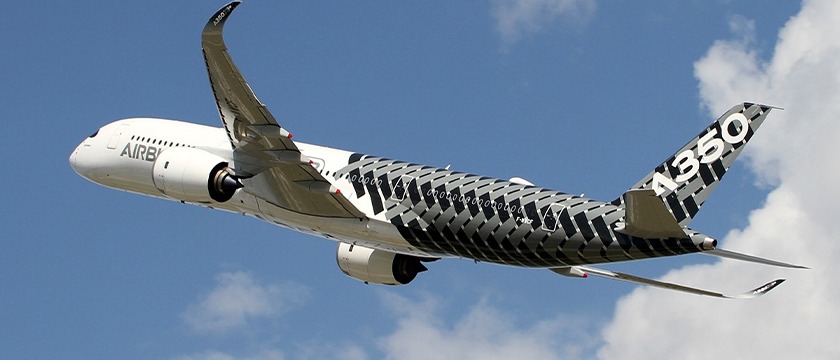
Introduce
In today’s rapidly developing aviation industry, materials science and technology have always been at the forefront, and their application in the aviation field is crucial to the performance, safety and economy of aircraft. As an emerging material type, advanced thermoplastic composites have attracted much attention in recent years and have shown great potential in the aviation field.
Advanced thermoplastic composite materials refer to materials with excellent performance and special functions that are made of two or more materials with different properties through compounding, molding and other processes. Its main components include thermoplastic resin matrix and reinforcing materials, such as carbon fiber, glass fiber, etc. Compared with traditional thermoset composite materials, thermoplastic composite materials have higher plasticity and processability, and can be processed multiple times by heating and reshaping, so they have wider application prospects.
This article will introduce and analyze the definition, characteristics and importance of advanced thermoplastic composite materials in the aviation field, aiming to explore its future development prospects.
Advantages of Advanced Thermoplastic Composites
Thermoplastic composites are one of the materials that have attracted much attention in the aerospace industry today, showing obvious advantages in terms of environmental protection, cost-effectiveness and performance advantages. The advantages of thermoplastic composite materials are obvious in terms of environmental protection characteristics, manufacturing cost and efficiency, and material performance superiority.
Environmentally friendly features
Thermoplastic composite materials are more environmentally friendly than traditional materials, such as metal and thermoset composite materials. The manufacturing process of traditional materials often produces a large amount of waste and harmful substances, causing serious pollution to the environment. Thermoplastic composite materials usually use renewable and recyclable materials, which produce less waste during the manufacturing process and can be recycled and reused, greatly reducing the impact on the environment. This is highly consistent with the trend of pursuing sustainable development in today’s society, making thermoplastic composite materials very popular in aviation applications.
Manufacturing costs and efficiency
Thermoplastic composites tend to be cheaper to manufacture than traditional materials. First of all, the manufacturing process of thermoplastic composite materials is relatively simple and has high production efficiency, which can significantly shorten the production cycle and reduce production costs. Secondly, due to the plasticity of thermoplastic composite materials, the one-piece molding process can be used during the manufacturing process, which avoids the need for multiple processing of traditional materials and further improves production efficiency. Therefore, in the aviation field, the wide application of thermoplastic composite materials can effectively reduce manufacturing costs and improve production efficiency, thus bringing greater economic benefits to aviation companies.
Material performance superiority
Thermoplastic composite materials have excellent mechanical properties and high temperature resistance, and can meet the requirements for material strength, stiffness and durability in the aviation field. At the same time, thermoplastic composite materials have high design flexibility and can be customized according to specific application requirements, further improving the performance advantages of the material. Therefore, thermoplastic composite materials not only have broad application prospects in the aviation field, but also show great development potential in other industrial fields.
With the continuous advancement of science and technology and the continuous innovation of material manufacturing processes, it is believed that thermoplastic composite materials will be more widely used in the future and bring greater development opportunities to the aviation industry.
Key ingredients in advanced thermoplastic composites
As an important material in the aviation field, the performance and characteristics of thermoplastic composites are affected by their key components. Resin matrix and continuous fibers are the two most critical components of thermoplastic composites. Their selection and characteristics directly affect the performance and application scope of the composite. In the development process of advanced thermoplastic composite materials, resin matrices such as polyetheretherketone (PEEK), polyetherimide (PEI) and polyphenylene sulfide (PPS), as well as continuous fibers such as high-strength fiber-reinforced composites, etc., plays a vital role.
Resin Matrix
- As a high-performance engineering plastic, polyetheretherketone (PEEK) has excellent high temperature resistance, chemical corrosion resistance and mechanical properties in thermoplastic composite materials, as well as good insulation properties and wear resistance. This makes PEEK widely used in the aviation field to manufacture high-temperature parts, structural parts and seals.
- Polyetherimide (PEI) has excellent mechanical properties, high temperature resistance and chemical corrosion resistance. It also has a high glass transition temperature and is suitable for manufacturing the resin matrix of high-performance composite materials.
- Polyphenylene sulfide (PPS) has excellent heat resistance, corrosion resistance and mechanical properties. It is an ideal high-temperature engineering plastic and is widely used in the manufacturing of parts in high-temperature environments such as aerospace engine parts and gas turbine blades.
The characteristics of these resin matrices enable thermoplastic composite materials to have excellent performance in harsh environments such as high temperature, high strength, and corrosion resistance, and meet the strict requirements of the aviation industry for materials.
Continuous Fiber
Secondly, the selection of continuous fibers is also crucial. High-strength fiber-reinforced composite materials have excellent mechanical properties and durability and are one of the commonly used reinforcement materials in thermoplastic composites. Common continuous fibers include carbon fiber, fiberglass and aramid fiber.
- Carbon fiber has extremely high specific strength and specific modulus, is light in weight, and has high stiffness. It is an ideal reinforcing material and is widely used in structural parts and aircraft components in the aerospace field.
- Fiberglass has good tensile strength and compressive strength and is a commonly used reinforcing material suitable for manufacturing the skeleton and structural parts of composite materials.
- Aramid fiber has excellent heat resistance, chemical corrosion resistance and mechanical properties. It is an ideal high-performance fiber and is widely used in high-temperature structural parts and protective parts in the aerospace field. The advantages of these high-strength fibers enable thermoplastic composites to have excellent tensile strength, flexural strength and impact resistance, meeting the stringent requirements for material strength and durability in the aerospace field.
Manufacturing Technology of Advanced
Thermoplastic Composites
In the manufacturing process of advanced thermoplastic composite materials, a variety of advanced technologies are used, including advanced thermoplastic composite prepreg manufacturing technology, automatic laying and in-situ consolidation forming technology, and welding technology.
Advanced thermoplastic composite prepreg manufacturing technology
Prepreg refers to a semi-finished product made by impregnating resin into fiber-reinforced materials and curing it. Prepreg manufacturing technology for advanced thermoplastic composites is one of the key links in their manufacturing process. Traditional thermosetting composite materials use resin impregnating agents to impregnate fibers and then solidify them. Thermoplastic composite materials use advanced prepreg manufacturing technology. The thermoplastic resin is heated to a molten state, then impregnated into fiber reinforced materials, and finally cooled and solidified to form a prepreg. This manufacturing technology has the advantages of simple operation, environmentally friendly process, and low cost. It can also realize automated production of prepregs, improving manufacturing efficiency and quality.
Automatic laying and in-situ consolidation forming technology
Automatic lay-up in-situ consolidation molding technology is an advanced composite molding process, especially suitable for the manufacture of thermoplastic composite materials. This technology achieves rapid and efficient production of composite parts by controlling the automatic laying of prepregs and then performing in-situ consolidation and molding under appropriate temperature and pressure. This technology can realize the integrated molding of components with complex structures, reduce subsequent processing steps, improve production efficiency, and at the same time ensure the molding quality and consistency of composite materials.
Welding Technology
In the aviation field, welding technology is usually used to connect composite structural parts. Welding technologies for thermoplastic composite materials include hot plate welding, ultrasonic welding, friction stir welding, etc. These welding techniques enable reliable connections between composite materials while maintaining their original properties and characteristics. Compared with traditional mechanical connection methods, welding technology has the advantages of high connection strength, light weight, and simple structure. It is suitable for the strict requirements on the strength and weight of structural parts in the aviation field.
The application of these manufacturing technologies not only improves the manufacturing efficiency and quality of composite materials, but also expands its application scope in the aviation field and promotes the development of the aviation industry.
Applications in the aviation field
Early Applications
In the early days, the aviation field mainly used metal materials to manufacture aircraft structural parts, such as aluminum alloys. However, with the continuous improvement of aircraft performance, safety and energy-saving requirements, traditional metal materials have gradually exposed their limitations, such as excessive weight and easy corrosion. Therefore, aerospace engineers began to explore new materials, among which thermoplastic composites have become one of the emerging materials that have attracted much attention.
Current Application Examples
At this stage, advanced thermoplastic composite materials have been widely used in the aviation field, especially in aircraft fuselage structures, wings, propeller hubs and other components.
- Fuselage structure: The application of advanced thermoplastic composite materials in aircraft fuselage structures has become a trend. Compared with traditional metal materials, thermoplastic composite materials have the advantages of light weight, high strength, and corrosion resistance. They can effectively reduce the overall weight of the aircraft and improve flight performance and fuel efficiency. At the same time, composite materials can also realize the integrated molding of complex structures, improving the design flexibility and production efficiency of aircraft.
- Wing: The wing is an important part of the aircraft. Its structure is complex and requires high material performance. The application of advanced thermoplastic composite materials in wings can reduce structural weight, improve the rigidity and fatigue life of the wing, and can also achieve a more aerodynamic design, reduce aerodynamic drag, and improve the flight performance and fuel efficiency of the aircraft.
- Propeller hub: Advanced thermoplastic composite materials are also widely used in rotor system components such as helicopter propeller hubs. Composite materials have good fatigue resistance and corrosion resistance, can meet the requirements of the rotor system under complex flight conditions, and improve the safety and reliability of helicopters.
Prospects
With the continuous development of aviation technology and the continuous improvement of aircraft performance, safety and energy-saving requirements, the application prospects of advanced thermoplastic composite materials in the aviation field are very broad. In the future, with the continuous innovation of manufacturing technology and the further improvement of material properties, the application of large composite structural parts will become an important development direction. For example, the application of large composite wings, fuselages and other structural parts will further reduce the overall weight of the aircraft, improve its flight performance and fuel efficiency, and promote the development of the aviation industry in a more environmentally friendly and efficient direction.
Development priorities and prospects
As one of the important materials in the aviation field, advanced thermoplastic composite materials are mainly focused on the development of high-performance prepreg manufacturing technology, the improvement of automatic laying and in-situ consolidation technology, and the development of automated structural welding technology.
Manufacturing technology development
High-performance thermoplastic prepreg is a key intermediate material for advanced thermoplastic composites. The quality and cost of prepreg largely determine the quality and cost of thermoplastic composites. Therefore, in order to realize the efficient application of advanced thermoplastic composite materials, we must first break through the thermoplastic resin melt viscosity control, prepreg equipment and prepreg process optimization technology to achieve high-quality manufacturing of high-performance thermoplastic prepregs.
Improvements in automatic laying and in-situ consolidation technology
The high-performance thermoplastic resin matrix has a high melting temperature and high melt viscosity. Hot press molding requires high temperature and high pressure, which requires large investments in molding equipment, high mold costs, and expensive auxiliary materials, resulting in many manufacturing defects and high manufacturing costs for composite structures. To improve the manufacturing quality and reduce manufacturing costs of advanced thermoplastic composite materials, it is necessary to develop advanced thermoplastic composite prepreg tape slitting technology and high-power laser heating automatic lay-up in-situ consolidation equipment, optimize automatic lay-up process parameters, and achieve advanced complex structures Automatic laying and rapid manufacturing of thermoplastic composite components.
Development of structural automated welding technology
The overall structure of advanced thermoplastic composite materials has better weight reduction efficiency. However, it is still difficult to achieve one-time molding of large-sized and complex thermoplastic composite components. Therefore, it is very urgent to develop efficient connection technology. The connection performance of thermoplastic composite materials has an important impact on the overall performance of the structure. The traditional mechanical connection and cemented connection methods are not suitable for advanced thermoplastic composite materials. It is necessary to develop advanced thermoplastics based on structural automated ultrasonic welding technology and resistance welding technology. Composite structure automated welding technology enables efficient connection of advanced thermoplastic composite materials.
In Conclusion
With the rapid development of the global aviation industry and the continuous advancement of technological innovation, advanced thermoplastic composite materials will show broader development prospects in the aviation field. In the future, it is expected that advanced thermoplastic composite materials will become one of the important materials in the aviation manufacturing industry and play an important role in energy conservation, environmental protection, lightweight, emerging application fields and global industrial chain integration, injecting new impetus into the development of the aviation industry.